Selecting Valves For Use With Chlorine
Valves in Chlorine Applications
Chlorine is used in processes from the production of PVC (polyvinyl chloride) to water treatment. In our modern culture chlorine plays a huge role in refrigeration; it enables us to cool our homes, our vehicles, and our food.
As a disinfectant, it makes drinking water and swimming pools safe by killing dangerous bacteria. It works as a sanitizer in eliminating bacteria from non-porous surfaces.
Chlorine is used to make paper, textiles, medicines, insecticides, and solvents. PVC is used everywhere from water pipes and insulation for electrical wires to blood bags.
When combined with water, it forms hydrochloric acid (HCl), a widely used and commercially important strong acid.
Under normal conditions, chlorine is a gas. Liquid chlorine has been pressurized and the temperature lowered.
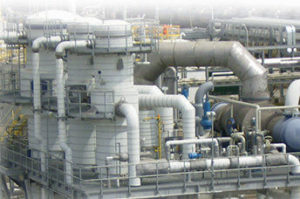
Materials Suitable for Chlorine Piping and Valves
Wet chlorine, that’s either gaseous or liquid chlorine having more than 150 parts per million of water by weight, is highly corrosive and will aggressively attack iron, steel, some stainless steel, Monel®, nickel, copper, brass, bronze, and lead. Dry chlorine can be handled by these metals at temperatures below 250°F without corrosion. And while titanium will react with dry chlorine causing corrosion or even combustion, it is a good option for wet chlorine.
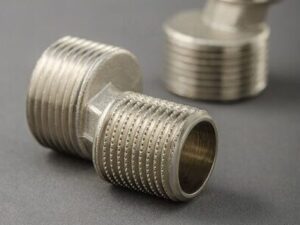
Risks Associated with Chlorine
Chlorine service comes with its share of risks. Some of the potential dangers and considerations are discussed here.
Expansion
In its liquid form, chlorine has a high coefficient of thermal expansion, meaning that the volume increases as temperature goes up. Care must be taken to ensure that any chlorine that gets caught between valves can be released into an expansion chamber. Otherwise, the pipes or fittings could burst or rupture due to the pressure generated by expansion of the chlorine.
Fire and Explosion
Chlorine is not flammable and does not, under normal conditions, support combustion. Because it is an oxidizer, however, care must be taken to avoid the potential of fire.
Oxygen cleaning of valves prior to installation and use is critical in chlorine applications. There can be no oil or grease residue or any other contaminant that could result in a fire in the valves or anywhere in the piping system. Processing in CPV’s class 10,000 clean room meets or exceeds the recommendations for manufacturers providing valves and fittings for chlorine use.
A co-product of chlorine that’s manufactured by electrolysis of sodium chloride solutions is hydrogen (H2). The hydrogen and chlorine gas mixture poses a risk of fire or explosion. Static electricity and impact, as well as ultraviolet light (from sunlight or elsewhere), can set off this reaction. These gases should not be allowed to mix.
Another potential by-product of chlorine manufacturing is nitrogen trichloride (NCl3), also known as trichloramine. This compound, which results from the reaction of chlorine and ammonium salts, irritates mucous membranes when inhaled. It’s also highly explosive.
Toxic
Liquid chlorine will burn the skin. When the liquid mixes with certain other chemicals, especially ammonia or acids, it releases toxic gases.
Gaseous chlorine is a strong irritant of mucous membranes. It’s also toxic at a level as low as 1000 parts per million.
Corrosive
Chlorine itself is non-corrosive. In its liquid form, however, it is hygroscopic, attracting water from its surroundings. With the addition of water, both the liquid and the gaseous chlorine states form hydrochloric (HCl) and hypochlorous (HClO) acids, making it highly corrosive. It can also form ferric chlorides (Cl3Fe), which is damaging to Teflon™ surfaces.
A moisture-free environment preventing water from entering the system will reduce or eliminate this risk. All equipment should be kept dry and care taken to ensure no water remains after cleaning.
Types of Valves for Chlorine Service
Some valve types are better than others when it comes to chlorine processes and operations.
Globe valves
Several factors make globe valves one of the best choices for chlorine use.
- Ability to provide a tight shutoff
- Ability to confirm whether it is open or closed
- The multi-turn operation that provides for slow and careful opening and closing
- Bi-directional seating – its ability to shut off in both directions without trapping liquid inside
Any leakage will allow moisture from the air to enter the system causing corrosion so flexible graphite or PTFE should be used for packing.
In accordance with The Chlorine Institute’s Pamphlet 6, Piping Systems for Dry Chlorine, Edition 16, globe valves for chlorine service should have a bolted bonnet with at least four bolts, a blow-out proof stem, either Stellite hard-facing metal seating or PTFE soft-seating, and an outside screw and yoke gland for external packing gland adjustment.
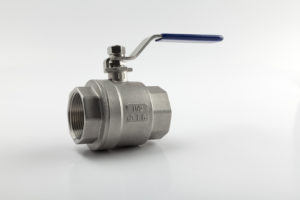
Ball valves
Providing tight shutoff, the ball valve has a reliable stem seal design. They can be full-bore or reduced-bore. A full-bore (or full-port) valve has an opening the same diameter as the piping, so there’s no restriction in flow through the valve.
Because chlorine that gets trapped in the valve could expand, ball valves need to have a release for any resulting pressure. Either a relief hole bored into the ball or pressure self-relieving seats can be used.
Single-seated segmental ball valves, on the other hand, do not trap liquid when they are closed. They’re commonly used as control valves.
Fully-lined ball valves are lined with a fluoropolymer resin, so there is no metal to chlorine contact. They can be used with wet or dry chlorine gas without concern for corrosion.
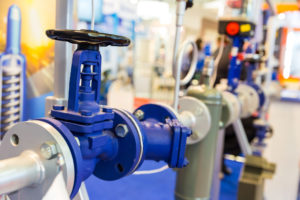
Butterfly valves
Both soft-seated high-performance butterfly valves and fully-lined butterfly valves are options. The soft-seated valves are useful in large pipes.
In fully-lined butterfly valves, like fully-lined ball valves, the fluoropolymer lining prevents the chlorine from touching any metal. They can be used with wet or dry chlorine.
Valve Selection Criteria
Stem seal
To prevent leakage through the stem seal in the presence of large or frequent temperature fluctuations, consider using bellows seals or live-loaded packing.
Temperature
Consider both ambient and processing temperatures when selecting valve materials. Keep in mind that throttling applications can create pressure differentials, resulting in lower temperatures.
Wet or dry chlorine
Wet chlorine is highly corrosive to a number of metals, whereas dry chlorine is not. If the chlorine being processed is dry but could become wet, select materials that are suitable for both.
Flashing and cavitation
The potential for flashing and cavitation should be considered and its avoidance considered when sizing the valve.
Contaminants
Where ferric chloride or sodium sulfate may be present, these compounds can build up in parts of valves where there’s low velocity. They also may adhere to some parts. Periodical stroking of the valve should free the build-up. Material that has been stuck for too long can harden, causing the valve to be unable to properly seal and to potentially leak.
All valves for use with chlorine service must be prepared for service according to The Chlorine Institute’s Pamphlet 6, Section 4.5 and labeled to show that it has met the requirements.
At CPV Manufacturing, we are unwavering in our commitment to quality. Browse CPV Manufacturing’s catalog or contact us to discuss your chlorine service needs.