Bring the Hammer to a Standstill—Silent Check Valves Protect Pumps and Pipes
A silent check valve, sometimes called a poppet check valve, non-return valve or even one-way valve, might have different names but they all supply the same function. This type of valve helps control and protect against pressure surges in water lines, or reverse flow, and the potentially devastating consequences or effects on pipes and pumps. When a pump pauses or stops and the flow of liquid also abruptly stops, this in turn stimulates high pressure shock waves that, if unchecked, can damage the pump and pipes. A silent check valve, when functioning properly, prevents these shock waves and the knocking or banging that signifies a water hammer phenomenon, thus protecting pumps, pipes and surrounding equipment.
The operation of a silent check valve hinges on a spring assisted disc, engineered to close the valve the instant the forward flow of liquid ceases. This prevents reverse flow to eliminate water hammer.
Consequences of a Water Hammer
Water hammer is a phenomenon that occurs when the pump shuts off and forward momentum propels the liquid on its course until offset by gravity or friction. When this happens and the liquid must suddenly either stop or change direction, this creates a shock wave or hydraulic surge. When a valve closes suddenly, and the water slams into it, this impact creates the water hammer that causes the knocking or banging sound inside a pipe after a pump abruptly shuts down.
Depending on the size of the column of liquid and its speed, the force of this momentum is powerful enough to cause serious damage to capital equipment, such as snapping the pump shaft or bursting the pump casing or pipes.
While this can occur during a single event, the effect can accumulate over time as the water hammer beats on the pump or the pipes, eventually resulting in ruptured pipes or a leak. This has the potential to create safety hazards for the workforce, damage surrounding equipment and/or cause extensive downtime and costly maintenance and repairs.
Other consequences besides water hammer could include over pressure from one side or potential contamination if the silent check valve is designed to prevent two different types of liquid from mixing together.
Silent Check Valve Construction
Design and materials for CPV Manufacturing’s silent check valves conforms to the ASME Boiler and Pressure Vessel Code. Standard valve bodies are cast of carbon steel with trim of either stainless steel or brass, however silent check valve bodies can be manufactured of bronze or cast iron as well. The choice of material depends on the potentially corrosive nature of the liquid the valves are designed to regulate.
CPV supplies check valves in a range of smaller sizes up to eight inches in diameter as the largest available. Most of in line piston style check valves are a low-pressure flange connection that meet the ANSI B16.5 flange bolt pattern, in class 125 to class 1500 (pressure).
Each has a spring-actuated disc that opens when flow starts and automatically closes when flow stops. The reliable checking action, designed and engineered into each valve, will not allow flowback. While a check valve isn’t a safety valve per se, it is critical to system performance and reliability.
All of the silent check valves manufacturing by CPV are fast closing, offering a:
- Sealing, bubble-type shut off
- Quiet operation
- Wide pressure range
- Broad temperature range
- Decades of leak-free and trouble-free operation
The full flow design offers good flow rates through CPV silent check valves, to minimize head loss and pressure loss. Both help increase the valve and overall system efficiency.
Description of Check Valve Features
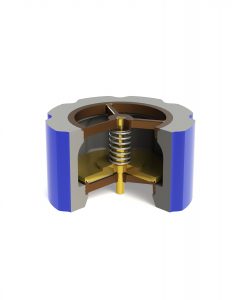
1. Helical Springs
These springs are engineered to ensure proper and complete valve closure automatically at zero velocity, when forward flow stops and before the beginning of reverse flow. CPV uses springs that can provide the lowest stiffness or K-factor consistent with optimum silent check valve operation. The springs are engineered for a conservatively estimated lifespan or performance of at least 10 million closures.
2. Guided Lift Design
A two-point bearing guides the disc with widely spaced bearings both above and below the seating surface. This eliminates any potential of the SCPV silent check valve disc tilting or becoming misaligned.
3. Full Flow Area
This design feature increases the valve’s efficiency and minimizes head loss.
Silent check valves are ubiquitous across industries and commercial buildings and compounds, found in pipelines and wherever there is a water system, including:
- Manufacturing or processing operations that use liquid or water
- Chemical processing
- Oil and gas industry
- Small communities
- Residential facilities
- Hospitals and universities
Work With Us
Companies in the market for silent check valves can count on CPV for reliability. It isn’t uncommon for silent check valves manufactured by CPV to have seen continuous service for 50 years or more. Once they are installed, it is a “set it and forget it” durable valve that will not need to be replaced for years, and supply trouble –free service in piping systems around the world.