Emissions Leaks
Testing for Fugitive Emissions in Pressure Relief Valves
Unintentional emissions of gases or vapors from pressurized equipment, or fugitive emissions, are more than an environmental concern. Besides the human health risks, pollution, and potential fines, they can hit the bank account more directly in the form of product loss.
A 2015 study as reported in Forbes, suggested that 3.6 trillion cubic feet or more of natural gas is inadvertently released every year. That’s an income loss of $30 billion plus.
Fugitive emissions consist of gases like methane, carbon dioxide, nitrous oxide, carbon monoxide, and sulfur dioxide, as well as more hazardous volatile organic compounds (VOCs) like benzene that present long-term health risks. In situations where large amounts of flammable liquids and gases are contained under pressure, leaks also bring an increased risk of fire and explosion.
Emissions leaks can come from numerous places, including pumps, seals, and flanges, with valves being among the highest sources of leakage from industrial activities at 75 percent. Of the valves responsible, about ten percent of fugitive emissions stem from pressure relief valves, the rest from control valves.
Pressure Relief Valve Emissions
Unlike control valves, pressure relief valves are self-actuated and self-contained. They open or close depending on the pressure within the system or line. When that pressure exceeds a maximum operating pressure, the pressure relief valve will open, releasing the excess gas into the air or atmosphere.
The pressure relief valve’s seats are subject to normal wear and tear. They also can become dirty, which will compromise the seal and lead to leakage with such leaks growing larger over time. There are no widely adopted standards (even within specific industries, such as oil and gas) for measuring or testing fugitive emissions from pressure relief valves.
In control valves, the packing is the focus of fugitive emissions, with certain types or styles of packing being much better at reducing emissions. Since pressure relief valves don’t have packing, fugitive emission compliance depends largely on factors like O-ring design, bolt torque, gasket seals, and the density and porosity of the valve materials.
Challenges of Emissions Testing
Although fugitive emissions come in multiple forms, the primary focus of emissions testing continues to be on methane, as methane emissions have the greatest impact on the atmosphere. But the question is, should methane be used for testing when such a test may result in more of the gas being released into the surrounding air? Many testing methods substitute helium for the methane. Because helium is a much smaller molecule, it will escape through spaces smaller than what would allow methane through. This brings up an even bigger question: what, if any, is the actual correlation between the two?
Leaks can be detected using several methods as well. While methane is best detected with a sniff test (the nose knows), either methane or helium can be detected with a sniff test, bagging (enclosing the valve to collect emissions), or a vacuum test.
Testing for Fugitive Emissions
Because there continues to be no common standard for testing pressure relief valves for fugitive emissions, currently used testing standards vary. There are governmental standards, standardization organizations (such as ISO), industry standards (such as API), and end-user guidelines (such as Shell and ChevronTexaco).
One method of testing uses control valve test standards as a starting point for pressure relief valves. These standards have both pressure and temperature cycling tests for liquid natural gas. It focuses the temperature cycling on the inlet of the valve using liquid nitrogen for the cold cycle and a heater for the hot cycle. The valve is fugitive emissions compliant if it passes the test from ambient to cryogenic back to ambient to high temperature and back to ambient. A sensor checks for gas leaks through the temperature cycle.
The second type of test uses a soap or detergent solution. When applied to a leak, bubbles will appear. However, with this method, there is no way to determine the amount or magnitude of the leak. The temperature of the equipment, as well as the size of the leak, will also affect results.
The EPA’s Method 21 allows for any portable instrument to be used for detection of emissions provided it meets certain criteria. One such test uses an organic vapor analyzer to measure total volatile organic compounds yielding numeric results. This does, however, sometimes give false positive or negative results and is more expensive to run than some other methods.
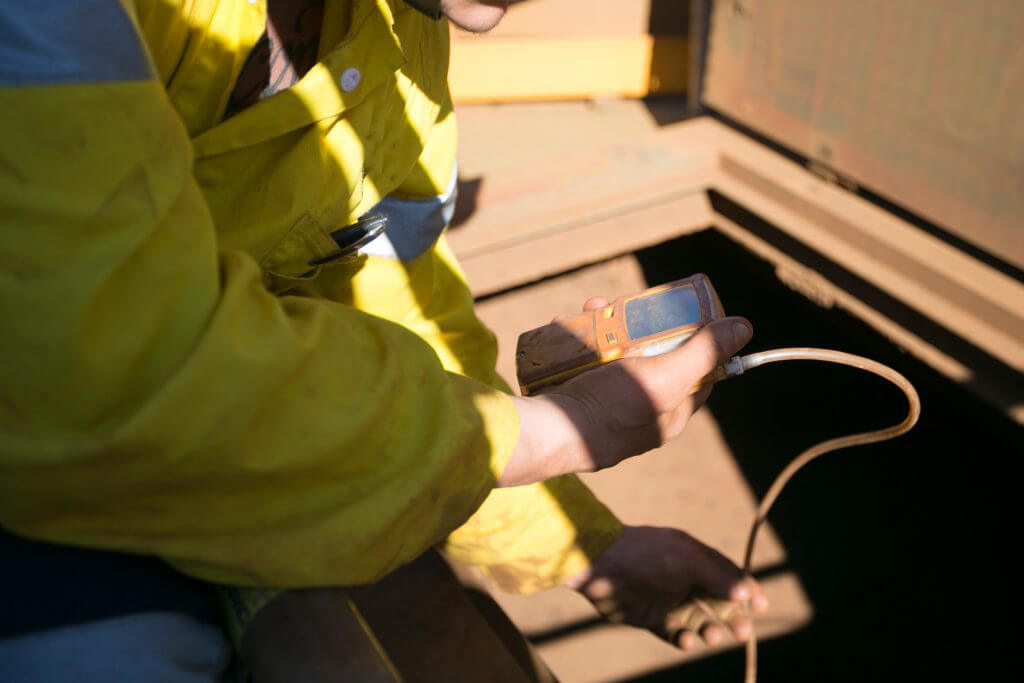
The ultrasonic test uses a portable device to detect ultrasonic sound produced by the escape of pressurized vapors. It’s less effective when in the vicinity of pneumatic actuated valves and must be within a certain physical range of the valve being tested. Although this method is capable of pinpointing individual leaks, too high of a concentration of leaks makes the individual location of emissions difficult.
Smart Leak Detection And Repair (LDAR) uses remote sensing technology to identify leaks. This technology uses a laser directed at the area to be scanned. A camera captures the image of the area with the escaping gas appearing as a black cloud. It provides accurate results with no false positives or negatives.
Remote Methane Leak Detection (RMLD) uses a laser-based natural gas sensor to identify leaks. It’s handheld and produces an audible alarm when it detects a high concentration or changing gas cloud.
Airborne Natural Gas Emission Lidar (ANGEL) detects natural gas in the atmosphere. It maps the location and quantities of gas emissions by plane, covering large geographic areas.
Be on the lookout for more formal standards from industry organizations such as API related to pressure relief valve fugitive emissions.
CPV pressure release valves for emissions testing are manufactured to meet or exceed the highest quality standards. Check out their full line of high-quality, American-engineered valves, including pressure relief valves.