Preventing Check Valve Failure – Best Practices
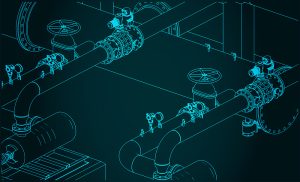
Check valves play the role of unsung hero, silently managing the unidirectional movement of substances and thwarting the menace of backflow. Check valves are found within the intricate web of industrial processes, where fluid and gas flow dictate the rhythm of operations. Yet despite its straightforward function, a check valve failure can unleash a cascade of consequences, from compromising system integrity to costly equipment damage.
Recognizing the pivotal role of check valves to maintain operational efficiency, process engineers can follow best industry practices to avoid check valve failure. This blog discusses how to recognize the purpose of check valves, identify symptoms of malfunction and explore underlying causes of failure.
What is the function of a check valve?
A check valve employs a straightforward yet effective mechanism to restrict flow within piping and equipment to a single direction. Typically, a check valve consists of a hinged or spring-loaded disc in the body. When gas or fluid flows in the desired direction, the pressure of the incoming flow pushes against the disc, causing it to open or move away from its seat, allowing the fluid to pass through the valve. This forward movement must be of a sufficient pressure to overcome the resistance of the spring and the weight of the disc.
However, in the event of reverse flow, the pressure differential causes the disc to close against the seat, preventing backflow. Stainless steel, brass, or bronze often serve as preferred materials for check valve fabrication. An O-ring helps seal the seat, and springs are used to aid with secure closure. This design serves to enhance the valve’s functionality and reliability for establishing one-directional flow and preventing backflow.
Many industries and processes rely on check valves including:
- Chemical processing
- Oil and Gas / Refining
- Industrial Gas
- Waste and wastewater treatment facilities
- Power generation
- Marine and shipbuilding
- Food and beverage
- Commercial HVAC and plumbing
What are the symptoms of a bad check valve?
- Leakage: One of the most common symptoms of a bad check valve is leakage, which can manifest as loss of pressure within the system or external leakage around the valve itself. This leakage may lead to inefficiencies in system operation and even potential safety hazards.
- Pressure Fluctuations: A malfunctioning check valve can result in deviations from normal operating pressure within the system. These fluctuations may indicate improper sealing or flow reversal, compromising system performance and stability.
- Visual Indicators: Corrosion, rust or debris accumulation on the exterior of the check valve can serve as visual indicators of potential internal issues. These signs suggest deterioration or damage to the valve components, affecting its functionality and reliability.
- Condensation or Wetness: Presence of condensation or wetness around the check valve may indicate leakage or improper sealing, leading to fluid bypass and potential system inefficiencies.
- Inconsistent Operation: Changes in the way the check valve operates, such as failure to open or close properly, can be indicative of internal damage or wear. These inconsistencies may disrupt fluid flow and compromise system integrity.
By recognizing these symptoms, operators can identify potential issues with check valves and take appropriate measures such as inspection, maintenance or replacement to ensure optimal system performance and reliability.
What are the primary causes of check valve failure?
Check valve failure can stem from either external factors or internal mechanisms. External factors such as extreme operating conditions, including high temperatures, pressure fluctuations or exposure to corrosive substances can accelerate material degradation and compromise the structural integrity of the valve components.
Initial material selection for a check valve should consider the environment and known or anticipated operating conditions, to avoid these issues and achieve a longer lifespan and reliable service. Select a high-quality material to prevent issues such as corrosion or metal fatigue.
Additionally, inadequate installation practices or improper system design may lead to misalignment, excessive stress or fluid turbulence, exacerbating wear and tear on the valve and contributing to premature failure.
Internally, mechanisms such as spring fatigue from excessive cycling or disc deformation over time can diminish the valve’s ability to maintain proper sealing and prevent backflow effectively. Moreover, the accumulation of debris, scale, or sediment within the valve can obstruct flow passages, impede valve movement, and ultimately lead to malfunction.
How can I reduce the risk of check valve failure?
A properly specified and installed check valve should last for several years. A check valve is one of the rare “set-it-and-forget-it” components that help ease maintenance responsibilities that also keeps capital equipment humming. Despite the general lack of maintenance these valves require, here is a short list of tips to help reduce the risk of failure.
- Proper Specification: This has been discussed, but since prevention is worth an ounce of cure, it’s worth mentioning again. Specify the proper materials for both the check valve and O-ring to avoid future problems, considering factors such as system temperature, pressure and gas composition.
- Maintenance: visually inspect the check valve and conduct pressure and temperature checks. Watch for signs (listed above) that might indicate an issue with the check valve, such as pressure loss.
- Component Replacement: Certain soft goods such as O-rings can wear out. Proactively replace these at any sign of wear, in adherence to manufacturer specifications to maintain optimal performance.
- Quality Assurance: Source check valves exclusively from reliable manufacturers with a reputation for quality, service and experience.
Check valves help maintain the integrity and efficiency of fluid systems across various industries to direct the flow in one direction and prevent backflow. Companies rely on CPV Manufacturing for valves due to its sole focus on the design, fabrication and modification of valves of various types that serve diverse industrial purposes.
Our soft-seated, bubble-tight shut-off meets or exceeds the most stringent industry standards, including the established ASME Boiler and Pressure Code. CPV’s spring-actuated check valve design responds swiftly and precisely to pressure changes, to prevent reverse flow and guard against pressure surges, to safeguard equipment and system lifespan. Enjoy leak-proof performance and protect your system from contamination with a check valve from CPV.