Valve Spacers
CPV Valve Spacers are the exact face-to-face dimension of CPV O-SEAL® valves. They can be used to protect valves during installation, and can be reused again and again for maintenance operations.
CPV O-SEAL® valves provide years of reliable service. However, the heat of welding or brazing during installation can compromise the cleanliness and/or integrity of the O-SEAL® valve. Using CPV’s hollow core valve spacers enables users to avoid that risk. These spacers replicate the exact face-to-face dimension of the O-SEAL® valve being installed. After welding or brazing has taken place, the entire system can be flushed. The spacer is then slipped out and the valve slipped in. Users are thus assured of both a perfect fit and a leak-proof connection for years to come. Moreover, once the O-SEAL® valve is in service, the valve spacer can be saved and re-used over and over again. For example, if flushing the system could cause problems or contaminate the O-SEAL® valves, users simply slip the valves out and slip the spacers in.
To order, enter the letter “F” in front of the part number for the CPV O-SEAL® valve you are installing. Be sure to specify the complete part number for each spacer you wish to order, including the size code or “dash” number. For example:
- F-380-3 (spacer for Globe Valve No. 380-3, size 1/2”)
- F-381-4 (spacer for Angle Valve No. 381-4, size 3/4”)
- F-123A-5 (spacer for Check Valve No. 123A-5, size 1”)
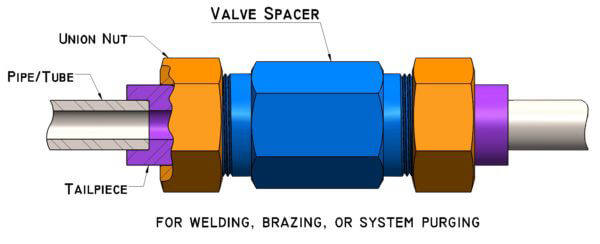