O-Ring Face Seal (ORFS) Technology: The Gold Standard for High-Pressure System Connections
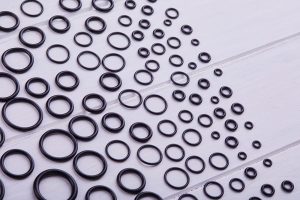
High-pressure fluid and gas systems require flawless connection integrity to prevent catastrophic failures and dangerous leaks. Even microscopic connection gaps can lead to significant issues. For example, hydrogen molecules, the most miniscule among common gases, can escape through tiny pores. High-pressure helium presents similar containment challenges due to its small atomic size and high mobility. Containment is an issue as the increased focus on decarbonization is pushing growth in hydrogen demand. Leaks not only create explosive hazards in the case of hydrogen and waste expensive gases like helium, but they can also compromise entire industrial processes, potentially leading to plant shutdowns and significant safety risks.
One answer to provide proper containment is O-Ring Face Seal (ORFS) technology, pioneered by CPV Manufacturing. This innovative sealing technology, featured in CPV’s O-SEAL® and Mark VIII® fitting lines, provides the appropriate sealing required for even the most challenging gases and fluids as well, used in the aerospace, petrochemical, alternative energy, semiconductor and multiple other industrial applications where even minor leaks can result in lost revenue and post severe safety implications.
Understanding ORFS Technology: A Revolutionary Design
ORFS technology employs a fundamentally different approach to sealing compared to traditional fitting designs. At its core, an ORFS fitting creates a seal by compressing an O-ring between two perfectly flat mating surfaces, secured by a union nut. This design principle represents a significant advancement over conventional fitting technologies, offering exceptional reliability through its elegant simplicity.
The key advantages of ORFS technology include:
- A self-energizing seal that improves under pressure
- Superior resistance to vibration and thermal cycling
- Protection of the O-ring from direct system media exposure
- Uniform compression across the entire sealing surface
Critical Design Elements That Ensure Performance
The effectiveness of ORFS technology relies on precise engineering considerations that work together to create a robust and reliable sealing system. The flat mating surfaces must be machined to exact specifications, with surface finish requirements that ensure optimal O-ring compression and sealing. This precision manufacturing prevents common failure modes like spiral failure or improper compression, which can be detrimental to tight seals in less sophisticated technologies.
The gland design represents another critical element in the ORFS system. Engineers carefully calculate and implement precise specifications for gland depth and geometry to achieve optimal performance. A properly designed gland prevents O-ring extrusion under high pressure, ensures appropriate compression ratios, maintains seal integrity during thermal cycling and protects the O-ring from installation damage.
Material selection also plays a vital role in system performance and longevity. The choice of O-ring material must account for the operating temperature range, chemical compatibility with system media, required durometer rating and anticipated environmental exposure conditions.
Exterior plating of the seal can help with its structural integrity, to help resist rust due to exposure. This comprehensive approach to material selection ensures that each component of the sealing system is optimized for its specific application.
The design and materials selected supply reliability and longevity of service under conditions that are often a major cause of component failure, such as:
- Temperature extremes (hot or cold)
- Corrosive or aggressive chemicals
- High pressure
- High vibration
CPV’s Industry-Leading ORFS Solutions
CPV Manufacturing has developed two distinct product lines that leverage their pioneering ORFS technology to meet diverse industry needs for a bubble tight seal. The O-SEAL® fitting line specifically targets high-pressure liquid and gas systems, finding extensive use in aerospace, industrial gas, drilling operations, petrochemical processing, and military applications. These industries demand unfailing reliability and superior performance under extreme conditions.
The Mark VIII® fitting line serves equally demanding applications in chemical processing, power and other industries. These fittings are engineered to provide exceptional performance in environments that require chemical compatibility and long-term reliability. Both product lines share fundamental design features that distinguish them from conventional fittings, including precision-machined flat mating surfaces with a protected O-ring groove and a union nut design that ensures proper compression.
Installation and System Design Requirements
Successful implementation of ORFS fittings requires attention to several critical factors:
- System design requirements (operating pressures, temperature ranges, material compatibility)
- Installation procedures (surface cleanliness, proper alignment, torque specifications)
- Maintenance considerations (accessibility, inspection protocols, O-ring replacement)
Long-Term Performance and Maintenance
When properly specified and installed, ORFS fittings provide exceptional long-term performance in critical applications. Regular visual inspections should check external surfaces for damage or corrosion, while system monitoring can identify any early signs of leakage. Periodic verification of torque settings and replacement of O-rings during scheduled system maintenance helps ensure continued reliable operation. Improper installation and under- or over-torquing are just two of the factors that can potentially cause O-ring failure in mechanical systems. Other causes can include:
- Compression set – Caused by elastomeric material failing to return to its original state after compression, or when it flattens.
- Extrusion and nibbling – This can occur for an O-ring that has edges which protrude outside of the sealed area.
- Spiral failure – Excessive compression can cut the O-ring, destroying the seal.
- Explosive decompression – This can occur when a high-pressure gas becomes trapped within the internal structure of the seal. As the gas expands to match external pressure, the O-ring can blister or rupture.
- Chemical degradation – Points out the importance of initial material selection, as incompatibility between chemical exposure and the O-ring elastomer causes degradation.
- Thermal degradation – Due to exceeding the high-temperature limit of the elastomeric material.
- Abrasion
Selecting the Right ORFS Fitting Solution
The development of ORFS technology by CPV Manufacturing marked a significant advancement in fluid system connection reliability. Through continued innovation and refinement, CPV’s O-SEAL® and Mark VIII® fitting lines represent the current state of the art in high-pressure connection technology for a bubble tight seal. When connection failure would prove detrimental to human safety or operational effectiveness, ORFS technology provides the industry’s most reliable sealing technology available for gas and fluid containment.
For more information about selecting the right ORFS fittings for your application, contact CPV Manufacturing’s technical support team at salesadm@cpvmfg.com.