Globe Valves Offer a World of Difference for Tighter Seals
Globe valves operate as a linear motion valve to stop, start and regulate flow. The design incorporates a disc-to-seat ring contact at a perpendicular or 45-degree angle, to regulate the flow of gas or liquid either under or above the disc and seat, depending on the application, allowing for a tight seal. This capability allows globe valves the flexibility for use in both high- and low-pressure applications and eliminates potential seat leakage.
This reliability and flexibility explain why at one time, globe valves were utilized across industries more than any other type. As valve designs evolved, new designs better suited for various applications replaced globe valves in some instances. However, for a tight regulation of flow, the globe valve performs better than other types of valves, such as gate or ball valves. Determine whether a globe valve will best suit your flow parameters and requirements, and the best applications for its use.
Globe Valve Design and Operation
As its name implies, a globe valve is constructed with a round or spherical body, plus a seated disc and a vertical stem. The flow inside the globe valve is regulated by this stem’s movement, either up or down. And depending on its operational position, either fully or partially open or closed, the globe valve regulates the liquid flow within a pipeline.
The seats are designed to line up parallel with the flow of the liquid, utilizing its force to help seat the disc for a tight seal, without leakage. The farther the disc is positioned away from the seat, the more fluid will flow through the valve. The globe valve’s design and construction make it an ideal component for high-pressure and high-temperature systems.
The Importance of Directional Flow in a Globe Valve
The reason globe valves can operate in a wide range of pressure and temperature applications has to do with the way the disc operates. Globe valves used in low-pressure and low-temperature applications are designed to have the pressure flow under the disc. This directional flow allows the disc to rotate freely on the valve stem. The free rotation and low-pressure application allow the disc to fit snugly against the seat as the valve closes, for less leakage.
When pressure flows above the seat in a high-pressure and/or high-temperature system, this helps prevent the stem from contracting as it cools down, and also keeps the disc from lifting off the seat. A globe valve body should have an arrow indicator to point to the valve flow direction.
Globe valves come in a range of sizes, depending on the pressure and flow required. These valves can be either air or electronically actuated for reliability and better regulation. This actuation gives the globe valve another advantage over other style valves, such as a gate valve, which can be heavy and difficult to turn.
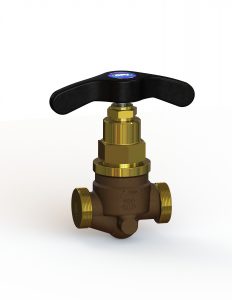
A globe valve can supply:
- Automated actuation (shutoff) for greater reliability
- A shorter stroke (compared to a gate valve)
- Ability to:
- operate under extreme temperatures, hot or cold
- regulate flow of abrasive or caustic substances
- regulate low- or high-pressure applications
- Wide range of material options
Typical applications or industries for use of a globe valve would include:
- Petrochemical for flow-regulated fuel oil systems
- Industrial gas applications
- Bulk filling in high pressure systems
- Water cooling systems
- Chemical feed systems
- Steam vents, boilers and drains
- Naval and commercial vessels (bilge suction or to prevent back flooding)
Types of Globe Valves Available
Globe Valve Design Based on Fluid Flow
The difference as explained earlier, is in the discs, and the method of closure or operation in accordance with the direction of the material flow, of either a gas or a liquid. A disc that closes against the direction of the flow offers a quick opening valve. Applications that require a quick closing valve might select a globe valve with a disc that closes with the direction of the flow.
Ball vs. Needle Disc Types
A ball disc globe valve is recommended for a low-pressure, low-temperature system. A needle disc is more often indicated for a high-pressure, high-temperature system
Z vs. Y Globe Valves
A Z style globe valve features a disc and seat that are perpendicular or sit at 90° to the pipe axis.
A Y-type of globe valve is designed to have the stem and seat of the valve at 45° to the pipe axis.
CPV Manufacturing offers its customers a wide range of globe valve sizes and material choices, with custom elements and design options available. CPV has the capability to design globe valves to handle specialty connections. Sealing integrity is built into any globe valve manufactured by CPV. For flexibility, reliability and a tight seal on a globe valve that will operate trouble-free for years, contact CPV Manufacturing today.