Pneumatic Valves: Matching Material to Gas Type Key for Performance
Pneumatic valves are used to control or modulate the flow of gas in a pneumatic system, to regulate the passage of gas into the various parts of this pneumatic system, whether tubing, piping or other devices. There are four main categories of pneumatic valve types, including directional, non-return, flow control and pressure control. CPV Manufacturing supplies the first three types of pneumatic valves, primarily for the regulation of industrial gases.
In addition to quality manufacturing of the valve itself, CPV Manufacturing developed its proprietary O-Seal® technology, which supplies a durable, soft-seat design for thousands of lifecycles of bubble-tight shutoff operation. While purchasing agents and operators need quality manufacture and the right material selection for the valve construction, the valve’s reliability for leak-proof operations relies on the O-rings and packings for proper sealing.
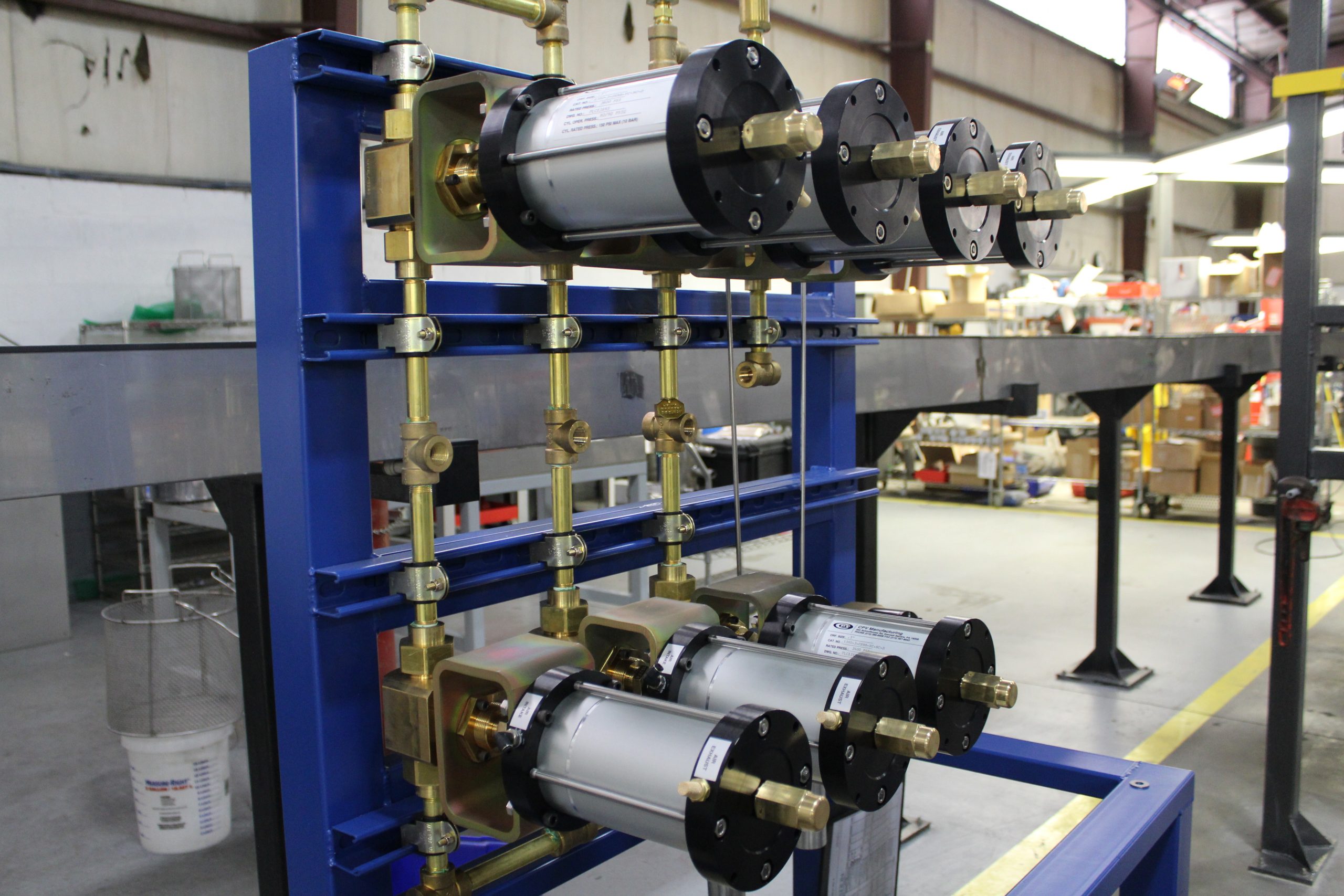
Pneumatic Valve Function/Types
Pure gas and mixed gas bottle filling of high-pressure gases require reliability and durability to avoid leakage. This same level of reliability and durability is critical for the hydraulic systems in steel mills and other heavy industries. To this end, CPV developed its FloMaster® pneumatic valves with a variety of engineered features.
CPV Manufacturing offers a wide size range and application-specific valves to suit multiple application scenarios. The products can be used in conjunction with each other, from more precise, regulated control to complete shut off.
The main industries that rely on high-pressure pneumatic valves would include:
- Gas industry for bulk filling applications
- Industrial gas manifolds
- Filling cylinders
- Control panels
- Hand valves
- Non-returns (check valves)
- Actuator valves
- Petrochemical Processing
- Refineries
- Distillation columns
- Cryogenic Gas Industry
Valves/Valve Material Selected According to Gas Type
Pneumatic valve materials selection is heavily dependent upon gas type and application. CPV Manufacturing carries different valves for the various types of gases, which are classified as elusive, inert, flammable, mixing gases or specialty gases.
The different types of gases, such as oxygen, hydrogen, helium, carbon dioxide, argon, etc., are matched up to individual valve product lines developed for those gases and their typical application scenarios. Specialty gases, which would also include electronic gases, require tight adherence to specifications to prevent leakage due to the dangers of flammability and toxicity.
High-tensile bronze and Naval Brass are the most common metals of choice for standard pneumatic valves manufactured by CPV Manufacturing. The valve material or metal selection depends on the type of gas it will encounter as well as other specifications for corrosion or oxidation resistance.
Overall, the four main types of materials or categories that can be employed for valve construction include:
- Stainless steel
- Brass (or bronze)
- Monel™
- Super alloys
Monel is a blend of 70% nickel with 30% copper, used for certain gases, such as high-pressure oxygen.
Super alloys can include Hastelloy or Inconel. Hastelloy provides excellent localized corrosion resistance, ease of welding and fabrication and often sees use for certain applications in the chemical processing industry and marine industry.
Inconel is part of a family of nickel-based super alloys, designed for high-heat environments that also require oxidation and corrosion resistance.
These super alloys and specialty metals are rarely used but are available when specifications warrant.
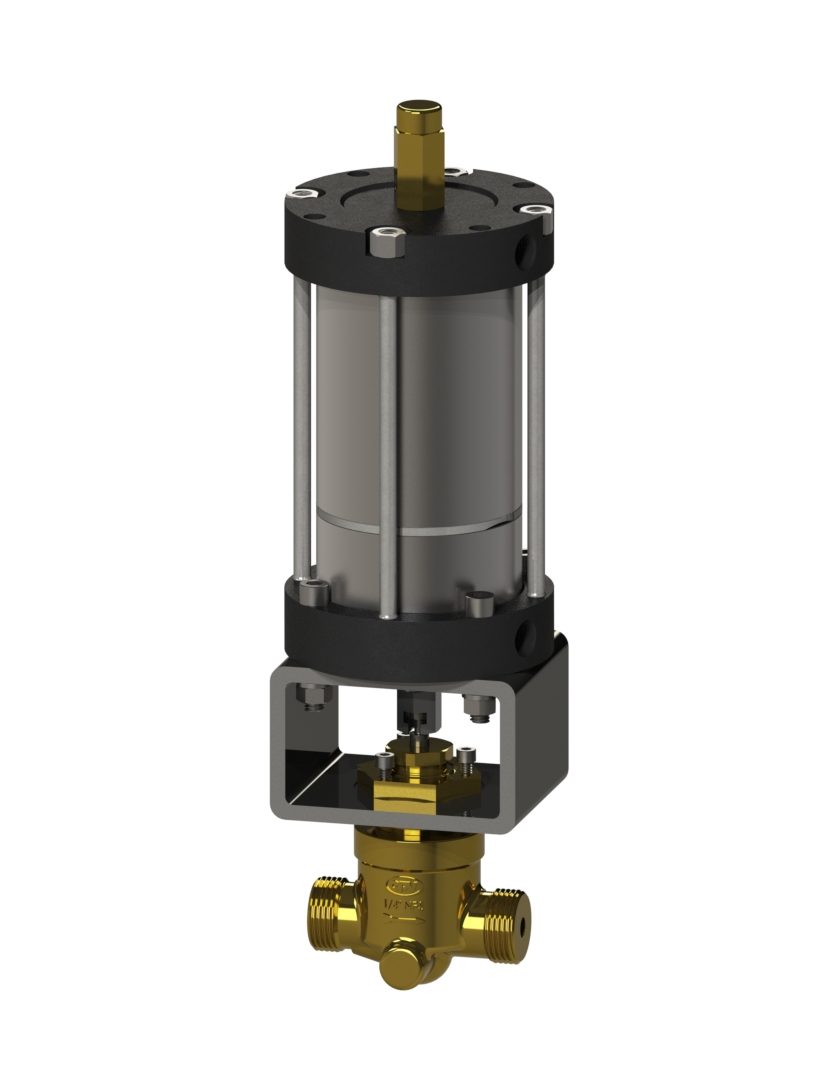
Linde Requires Pneumatic Valves for Specialty Gas Filling Station
As one example of specialty gas containment, a Linde facility in Santo Domingo, Mexico requires valves for a specialty gas filling station that could help regulate more than 250 gas mixes for a variety of applications in the industrial, medical and welding industries. Linde specifically requested CPV valves and fittings. Air-actuated FloMaster® O-Seal® valves were installed on all 18 automated heads on the platform.
In addition, CPV valves were used to achieve instantaneous open/close operation on each of 18 separate filling locations controlled by these automated heads. The use of overall, 180 CPV O-Seal valves combined with state-of-the-art computer controls, enabled this Linde gas filling station to complete 360 separate gas mix orders simultaneously. All CPV O-Seal® valves are leakproof even when used to control elusive gases such as helium or hydrogen.
Soft Goods: The Key to Reliability
The soft materials, or the elastomeric O-rings and packing materials, directly influence the internal and external sealing and help control gas flow. The reliability of the seal for the pneumatic valve, to prevent leakage, is dependent on the soft material selection and its specification is determined by the nature of the gases requiring regulation, as well as temperature and pressure of the gas.
For example, acetylene is both caustic and flammable, with trace amounts of other gases, and there is a specific type of elastomeric material suitable for the O-ring and packing (a stem seal) for proper sealing to prevent acetylene from leaking.
O-Rings and elastomeric material selection help prevent “fugitive emissions,” or the unintentional leakage of gases or vapors from pressurized equipment and its components, such as piping flanges, storage tanks, compressors, or valves. Multiple points within a processing facility can act as the source of potential leaks.
Fugitive emissions can result in significant consequences and their containment provides operators with a number of benefits including:
- Preserving worker health and safety
- Preventing environmental damage related to air pollution or the greenhouse effect
- Avoiding costs for unplanned maintenance or plant downtime
- Protecting profitability by avoiding the economic cost of lost commodities
Valve design will contain the gas or fluids within the system and should be able to withstand the purging or vacuum service of the system or cylinders.
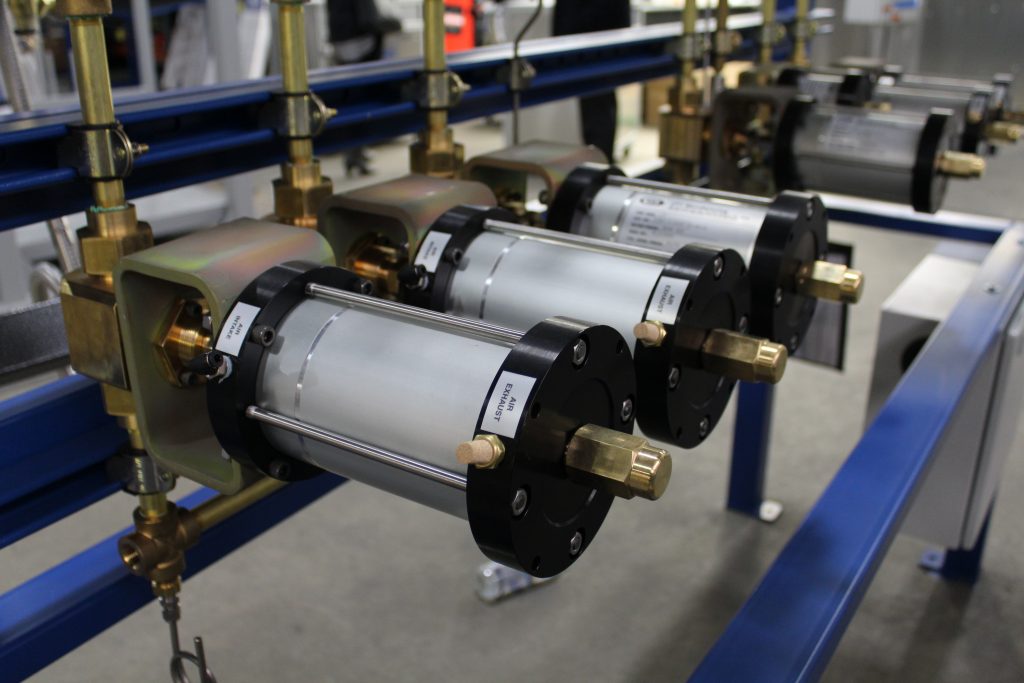
Pneumatic Valve Specifications
- Gas type—determines the elastomers selected for the soft materials (O-rings and packing) and in certain cases, the type of metal for the valve itself
- Application
- Temperature—both internal for the gas and the external environmental temperature
- Automated or manually operated
- Flow coefficient (Cv) as a measure of the valve’s capacity for air flow
- Pressure—operating pressure or pressure range the valve is rated to handle, in Bars or psi
- Port size and thread connection type
- Valve cycles, representing the highest number of cycles the valve can handle in a specified time span
- Ability to withstand purging and vacuum service
Most customers within the industrial gas industry know their products well. The major frustration is finding a supplier with quality manufactured valves that will not leak. CPV Manufacturing offers experience with valves and fittings that date to the 1950s, with continuous engineered improvements and customization when required.
Each valve is tested in house prior to shipping. Trust CPV Manufacturing for leakproof, quality manufactured pneumatic valves to suit any type of gas. Contact us today.