Mark VIII® Direct Weld/Braze Fittings Prove Reliable in Tight Spaces
Look to Welding and Brazing Options When Leak Proof Fittings are a Necessity
Many valves manufactured by CPV provide leak protection via an O-ring, to supply critical seals within high pressure environments. While greatly reliable, certain applications require an even stronger degree of leak-proof security and in this instance, the best choice might be a welded connection, such as CPV’s Mark VIII® direct weld/braze fittings. This fitting was designed for tight spaces and can be heat sealed for critical applications via welding, orbital welding or brazing. Find out when to specify a welded fitting like the Mark VIII® direct weld/braze, designed for pressures from vacuum up to 6000 PSI.
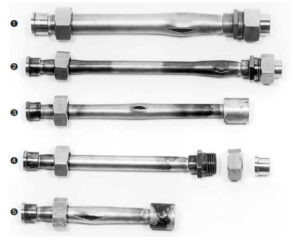
Welded Fittings Supply Permanent, Leak-tight Seals
Welded fittings can be considered superior to O-ring joins for a few reasons. The weld creates a permanent, leak-tight seal that cannot be loosened, while the best O-ring seals can wear out or degrade over time, leading to leaks. In addition, welded fittings can withstand higher pressure and temperature ratings, generally, compared to O-ring joins. Finally, welded fittings are better able to resist vibration and/or mechanical stress, for a robust join that will supply a longer lifespan than an O-ring connection.
Space constraints are another factor. When they dictate fewer parts or more narrow fittings, or the connection will be located in an area difficult to service, a welded fitting supplies a permanent connection for these small spaces.
Other applications that might demand a hermetically sealed, leakproof fitting can involve hazardous, flammable, toxic or even costly substances. In these instances, operations require a hermetically sealed fitting to protect worker safety, the environment, surrounding equipment or to try to minimize material losses to maximize the return on investment. As one example, in nuclear power plant instrument lines, tubing connections are most often welded, to withstand both temperature surges and pressure variations, and is one example of an application for Mark VIII® direct weld/braze fittings.
Potential use case scenarios for Mark VIII® direct weld/braze fittings:
- Shipboard or maritime applications
- Power plants other than nuclear
- Industrial gas filling operations
- Critical life support systems in aerospace and undersea apparatus
- Marine-based oil and gas drilling systems’ hydraulic controls (in blowout preventer stacks)
Weld Standards and Benefits of Welded Joints
Customers are responsible for adhering to industry standards for welding within the application environments governed by the nuclear industry, or Department of Defense for naval shipboard use, for example. Brazing offers the option to make a more permanent connection when joining dissimilar metals, while welding forms a bond between metals of the same type.
A welded fitting offers a greater degree of structural integrity compared to a metal-to-metal fitting or even a joint connection using an O-ring seal, with the weld creating a hermetic seal against leakage, as long as the weld is properly done. Leak testing is always recommended for a welded joint or fitting.
CPV offers step-by-step instructions for brazing in a tutorial with a photo guide illustrating the process. Find that resource here.
Options for Mark VIII® direct weld/braze Fittings
Mark VIII® direct weld/braze fittings are available in stainless steel as well as various specialty alloys or metals, such as brass or Monel®. Specifications should include:
- Outer dimension
- Pressure rating
- Wall thickness
- Temperature ranges
- Connection sizes
CPV’s main product line for direct weld fittings ranges from an eighth inch to a two-inch outer diameter. The easy connect/disconnect tube fittings connect without swivel joints, for another Mark VIII® advantage.
Mark VIII® welded fittings replace the leakage prone metal-to-metal sealing of an ordinary hose end connection with positive O-ring sealing. For a permanent branch line, the Mark VIII® direct weld/braze fitting supplies an economical leakproof means of making the connection with the direct weld/braze elbow allowing operators to avoid making a 90-degree bend in a tube, which can crimp the tube decreasing material flow capabilities or stress the metal.
The Mark VIII® direct weld/braze socket is available in various configurations including direct couplings, elbows (including 90 and 180-degree bends), a Tee connection and o-ring face seal unions. The fittings supply a cost-effective solution for tight fitting joins or a permanent branch line. In addition, the fittings adapt easily to a vast library of valve types, sizes and configurations, available from CPV, for a single source supplier.
CPV keeps Mark VIII® direct weld/braze fittings and its selection of valves in stock, for a quick turnaround. It offers size changes in the form of reducers or increases to meet custom connection sizes when required.
Trust CPV’s vast experience when requiring a fitting designed for weld and braze applications, to supply a permanent, hermetically sealed connection in critical applications for maritime use, power plants, industrial gas operations and manufacturing. For more information, visit our main company site at www.cpvmfg.com.